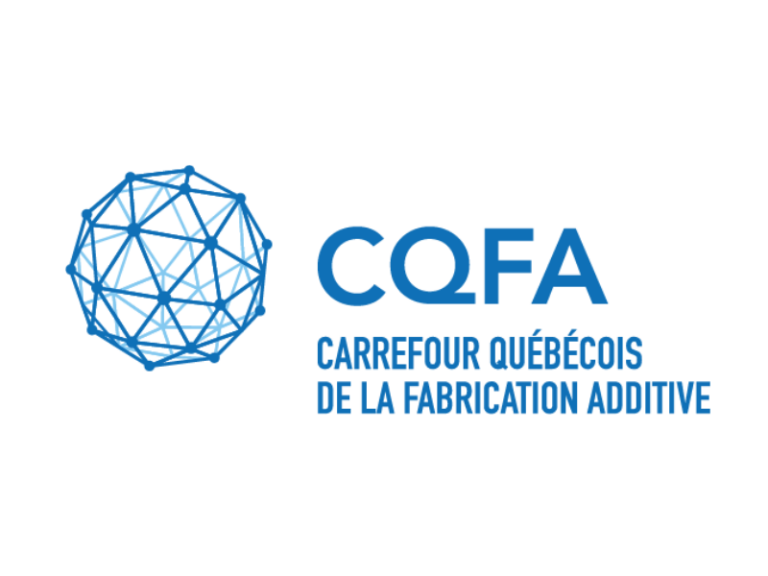
2023/11/14
Multi-scale model to simulate stress directionality in laser powder bed fusion: Application to thin-wall part failure
Tangestani, R.; Chakraborty, A.; Sabiston, T.; Yuan, L.; Ghasri-Khouzani, M.; Martin, E. (2023). Multi-scale model to simulate stress directionality in laser powder bed fusion: Application to thin-wall part failure. Materials & Design, vol. 22, August 2023, 112147.
In this study, line heat inputs are lumped to improve the computational efficiency while preserving stress directionality in laser powder bed fusion (LPBF). The lumped hybrid line (LHL) model predicts part distortion accurately within 10 µm of the experimental error in reasonable time. The effects of part geometry and scanning strategies on part distortion and failure during LPBF of thin-wall components are evaluated. Eight different printing patterns including different vector lengths and interlayer scan rotations for five different part lengths are studied. Simulation results show that the compressive stresses in the longitudinal and build directions create buckling, which limits subsequent layer deposition. This causes in-process part failure called the limiting build height (LBH) effect. A strong correlation between the vector length and residual stresses is shown. Longer vector lengths generate smaller compressive residual stresses along the build direction while inter-layer scan rotations homogenize the internal stresses in the scanning plane. Increasing the vector length and introducing scan rotations are useful processing strategies to improve the LBH. Moreover, part failure can be mitigated by varying the part geometry. Increasing the part thickness reduces the susceptibility to buckling and increases the LBH, whereas part length alters the failure mode.