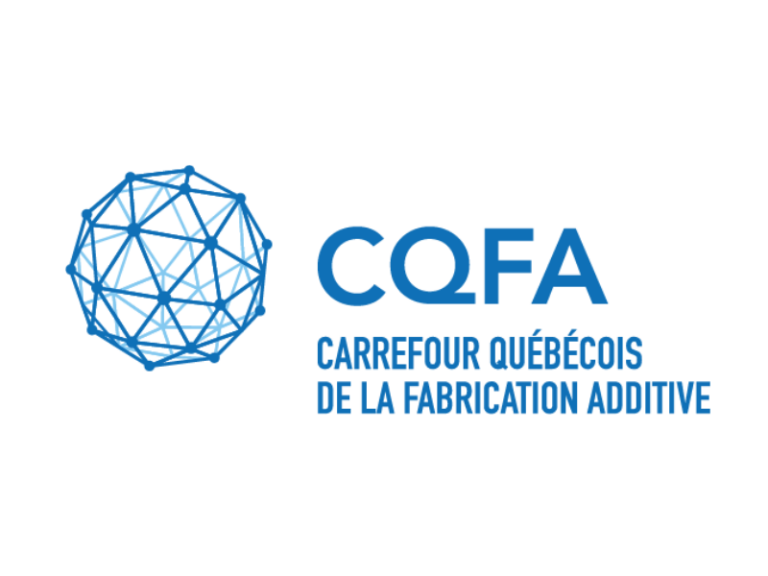
2023/02/08
Design, fabrication and validation of a 3D printer for processing powder-binder feedstock
Miclette, O. (2022). Design, fabrication and validation of a 3D printer for processing powder-binder feedstock. Thesis.
Material Extrusion Additive Manufacturing of highly-filled polymers (MEAM-HP) is a recent process that allows dense metal parts to be manufactured in four steps. The shaping of the part is carried out by 3D printing where the molten feedstock is deposited by a nozzle on a build platform in a manner similar to the fused filament fabrication process for polymers. Several studies focus on optimizing printing parameters with the aim of eliminating interlayer defects. These defects located at the junction of the printing lines are in fact holes which decrease the density of the parts and negatively affect the mechanical properties. Optimizing the print parameters reduces the size of these defects, but does not completely eliminate them. Few studies have investigated the use of low-viscosity feedstocks, which have the potential to reduce the occurrence of defects by allowing the feedstock to better conform to the shape of previously deposited print lines. This work aims to develop a new printer capable of printing parts using low-viscosity powder-binder feedstocks, demonstrate its performance and ultimately confirm whether the use of such low-viscosity mixtures can reduce or even eliminate interlayer defects. First, a printer with a piston extruder was designed and built. Then, the precision of movement of the build platform and the control of the extruder flow rate were validated. Next, the extrusion and build platform temperature as well as the extruder retraction volume were optimized to reduce print defects. Afterwards, six complex parts were printed to determine if low-viscosity feedstocks can be used for printing functional parts. The feedstock used in this study is composed of 65 vol. % 17-4PH stainless steel powder, 23 vol. % paraffin wax, 10 vol. % ethylene vinyl acetate and 2 vol. % stearic acid. During the preparation of the mixture, mixing under vacuum for one minute was sufficient to reach the maximum relative density of 99.8%, i.e. 1.2% more than that without degassing. The optimal retraction volume to avoid oozing through the nozzle when the extruder is stopped and to precisely control the starts and stops of the extrusion sequences is 3.6 mm3 . The extrusion and print surface temperature of 85°C and 52.5°C respectively helped eliminate outer and interlayer defects on a single printed part. During these prints, a novel technique of overlapping print lines was used to eliminate the presence of interlayer defects. Finally, printed parts with features such as thin walls, 45° walls, unsupported areas and complex surfaces demonstrated that low viscosity feedstocks can be used in the MEAM-HP process.