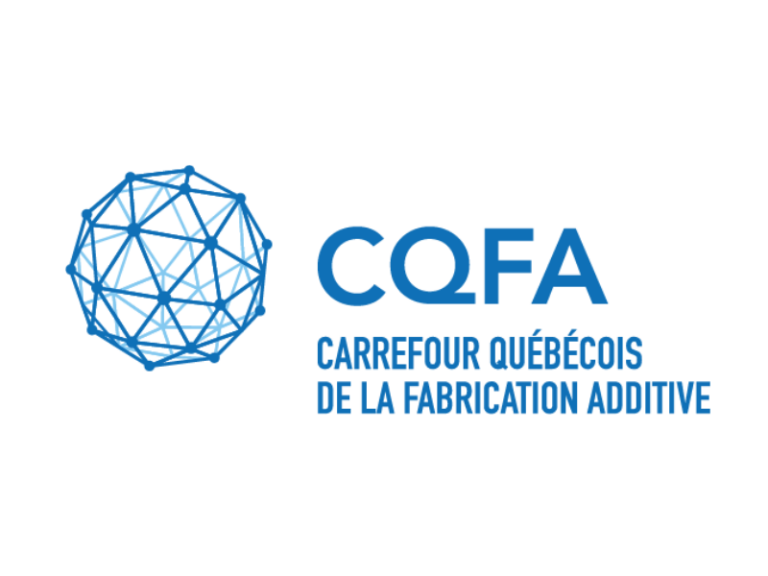
2023/05/10
Weldability of 316L Parts Produced by Metal Additive Manufacturing
Selmi H.; Brousseau, J.; Caron-Guillemette G.; Goulet, S.; Desjardins, J.; Belzile, C. (2023). Weldability of 316L Parts Produced by Metal Additive Manufacturing. J. Manuf. Mater. Process. 2023, 7 (2), 71.
The processes of metal additive manufacturing (AM) are no longer confined to rapid prototyping applications and are seeing increasing use in many fields for the production of tools and finished products. The ability to design parts with practically zero waste, high precision, complex geometry, and on-demand fabrication are among the advantages of this manufacturing approach. One of the drawbacks of this technique is the productivity rate, as the parts are made layer by layer, which also increases the production cost. Moreover, even the working space is limited, especially for the powder bed fusion technique. In view of these disadvantages and in order to guarantee the profitability of this process, it should be oriented to the production of complex components that have a limited volume with a design adapted to additive manufacturing. One solution with which to circumvent these drawbacks is to combine the 3D printing process with conventional manufacturing processes. When designing products, one may choose to use additive manufacturing to create locally complex parts and assemble them with parts produced by conventional processes. On the other hand, and due to the limited AM printing chamber space, it may be necessary to print large parts in multiple smaller parts and then assemble them. In order to investigate the weldability of stainless steel 316L parts produced by laser powder bed fusion (L-PBF), the mechanical behavior of different welding assemblies is tested. Five configurations are studied: non-welded AM specimens, two AM parts welded together, one AM part and one laser cut part welded together, two laser-cut parts welded together, and non-welded laser cut specimens. Welding is performed using the Pulsed Gas Metal Arc Welding process (GMAW-P). Specimen strength is assessed through static and fatigue tests. The results demonstrate that 316L AM parts are weldable, and the tensile and fatigue properties of L-PBF 316L welded components and welded laser cut components are comparable. GMAW-P welding led to lower fatigue results for AM components than for other configurations, but the difference is not important. It was observed that welding defects may have a direct impact on mechanical properties.