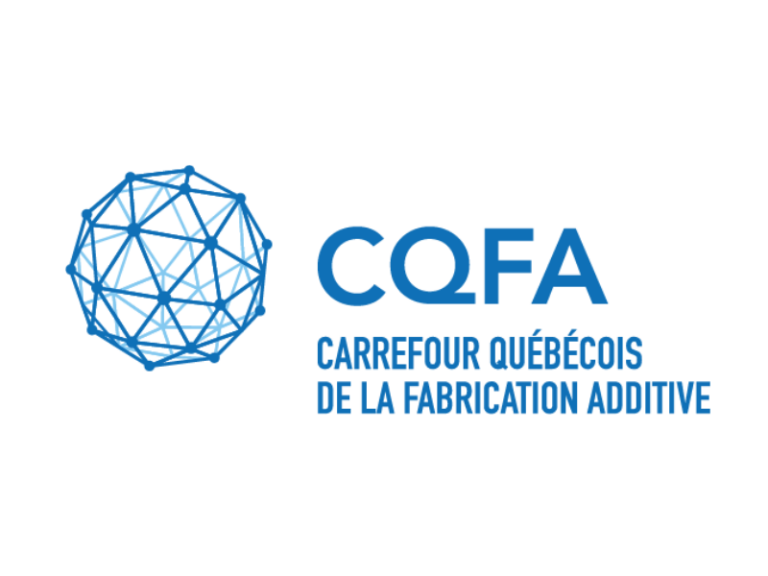
2023/02/13
Laser powder bed fusion of precipitation-hardened rene 41 and rene 77 nickel base superalloys
Atabay, S. (2022). Laser powder bed fusion of precipitation-hardened rene 41 and rene 77 nickel base superalloys. Thesis.
Laser powder bed fusion (LPBF) is a promising technology that enables production of complex parts with unique freedom in design and short lead times. For applications requiring high strength and high temperature resistance, Ni-base superalloys are the primary choice of materials. Although variety of superalloys can be produced through LPBF, most high strength alloys are prone to cracking and considered difficult to weld. The main objective of this research is to assess the processability of precipitation hardenable Ni-base superalloys by LPBF. For this purpose, processing of two different precipitation hardenable alloys, Rene 41 (R41) having a fair weldability and Rene 77 (R77) categorized as difficult to weld, are studied along with their microstructural development and mechanical properties. First, R41 alloy was produced by LPBF, and its microstructural evolution was investigated. Crack-free, dense samples were produced upon parameter optimization. The as-built (AB) microstructure revealed columnar grains with a preferred orientation along <100> direction. γ’ precipitation was suppressed due to high cooling rates in LPBF. Afterwards, the samples were subjected to the standard heat treatment (HT). Even though the grain morphology was similar to the AB sample, formation of carbide particles was observed along with the precipitation of γ’ after the HT. Mechanical properties of the samples both in AB and HT state was characterized. Results proved that when standard HT is applied to the LPBF fabricated R41 parts, the measured room temperature (RT) strength and elongation meet the AMS specifications. Effect of build direction on the mechanical properties was also studied. Since the microstructure obtained after LPBF is very different compared to the conventional processing techniques, suitability of the commercially applied HT cycles has to be studied. Hence, additional HTs were applied to understand the effect of different solutionizing temperatures on the development of microstructure and mechanical properties. Detailed microstructural analysis were conducted after each HT. These analyses revealed that for HT above the γ’ solvus temperature, resulted in the precipitation of γ’ and carbide phases similarly to the sub-solvus HT but with a different size distribution and morphology. However, formation of an equiaxed grain morphology with random orientation was detected. Furthermore, tensile properties were tested at 760°C. YS and UTS values obtained for AB, sub-solvus and super-solvus HT samples were on par with the wrought and HT alloys reported in literature. However, the measured elongation and deformation behaviors showed significant differences. The columnar grain morphology of the sub-solvus HT sample led to the highest elongation while the microstructure obtained after super-solvus treatment had the highest work hardening rate during deformation. Finally, the knowledge gained from R41 was used to study the manufacturability of the R77 alloy. This alloy is more prone to cracking during fabrication due to its higher content of alloying elements. Elimination of cracking in a difficult to weld alloy solely by parameter optimization was proven possible with LPBF of R77. Furthermore, these crack-free structures were maintained upon a modified version of the standard HT. Detailed microstructural characterization of AB and HT samples were conducted similarly to the R41. In this case, presence of extremely fine γ’ precipitates were identified after LPBF, and a bimodal distribution of precipitates was developed following the HT. Tensile properties for both conditions were tested at RT and 810 °C and the results were compared with wrought counterparts and with other difficult to weld alloys fabricated by LPBF. The deformation behavior of the samples in both conditions changed with the temperature. AB sample showed significant hardening whereas, the HT one had improved elongation due to thermally activated microtwinning.