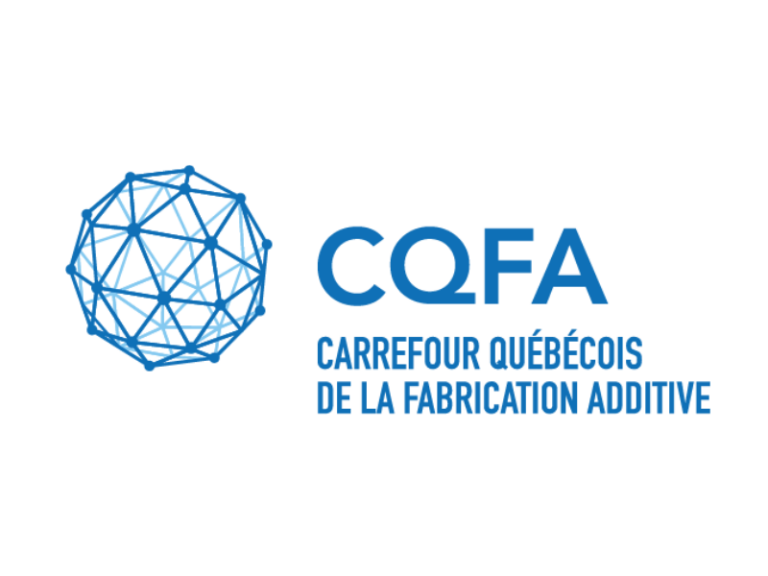
2023/02/15
Material Extrusion Additive Manufacturing of Low-Viscosity Metallic Feedstocks: Performances of the Plunger-Based Approach
Demers, V.; Miclette, O.; Côté, R.; Brailovski, V. (2022). Material Extrusion Additive Manufacturing of Low-Viscosity Metallic Feedstocks: Performances of the Plunger-Based Approach. Preprint.
In recent years, increasing attention has been directed at the material extrusion additive manufacturing of highly-filled polymers (MEAM-HP). This is because conventional polymer 3D printers, which are low cost and readily available, can easily be adapted for use with metal powder-filled polymer filaments. However, fabricating the latter is time-consuming and their formulations differ from regular MIM feedstocks by lower powder solids loadings and higher elastomer contents, thus requiring significant efforts to optimize their debinding and sintering conditions. Favorably, other types of MEAM-HP printers, such as screw- and piston-based ones, can process available MIM feedstocks and apply the debinding and sintering procedures that have already been optimized. In this study, a novel ram extruder-based printer with a 100 mm-diameter ― 250 mm-high build volume was developed to print a low-viscosity MIM feedstock composed of 65% of 17-4PH powder, 23% of paraffin wax, 10% of ethylene vinyl acetate and 2% of stearic acid (all in vol. %). The printer calibration and the process optimization procedures are detailed herein. The kinematic accuracy of the build platform revealed a maximum deviation of 29 and 92 µm in the vertical (Z) and horizontal (XY) directions, respectively. Prior to printing, a relative feedstock density of 99.8% was obtained using a one-minute degassing procedure. During printing, a 52.5°C build platform temperature was used and an 85°C extrusion temperature conferred to the feedstock a viscosity of 142 Pa·s at a shear strain rate of 180 s -1 (Ø0.4 mm E3D V6 nozzle, 1 mm 3 /s flow rate). Indirect measurements of the extrusion pressure using a load cell positioned under the piston allowed to maximize the accuracy of start/stop extrusion sequences by adjusting the retraction volumes. An overlap printing path technique was introduced to eliminate typical MEAM voids between printed lines. Finally, six parts exhibiting complex geometries were printed to validate the capacity of the printer to produce functional components using conventional low-viscosity MIM feedstocks.