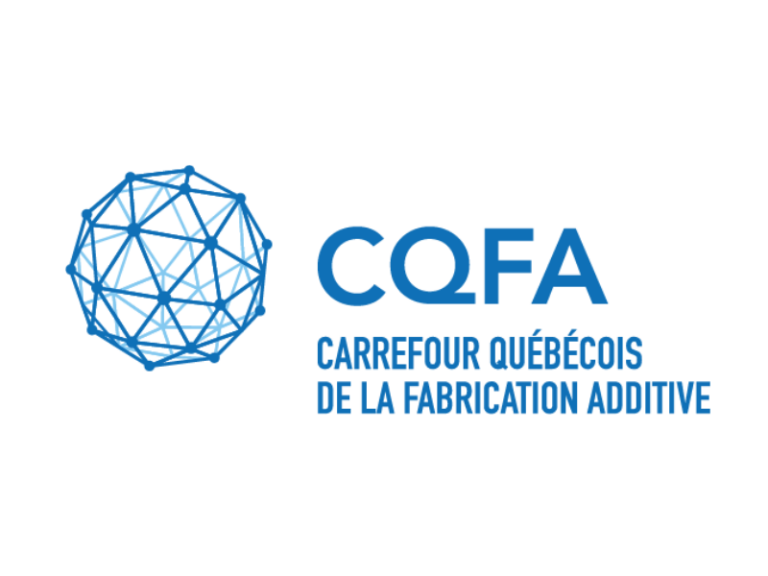
2023/01/17
Microstructure and Mechanical Properties of Ti-6Al-4V Additively Manufactured by Electron Beam Melting with 3D Part Nesting and Powder Reuse Influences
Wanjara, P.; Backman, D.; Sikan, F.; Gholipour, J.; Amos, R.; Patnaik, P.; Brochu, M. (2022). Microstructure and Mechanical Properties of Ti-6Al-4V Additively Manufactured by Electron Beam Melting with 3D Part Nesting and Powder Reuse Influences. Journal of Manufacturing and Materials Processing. 2022, 6(1), 21.
To better support the transition to more industrial uses of additive manufacturing, this study examined the use of an Arcam Q20+ industrial 3D printer for producing heavily nested Ti-6Al-4V parts with both in specification (IS) and out of specification (OS) oxygen content in reused grade 5 powder chemistries. Both the OS and IS powder chemistries were evaluated to understand their impact on build integrity and on static and fatigue performance. The results from our evaluations showed that controlling the bed preheat temperature in the Q20+ to relatively low values (326–556 °C) was effective in limiting microstructural coarsening during the long build time and enabled adequate/balanced performance vis à vis the tensile strength and ductility. Overall, the tensile properties of the IS Ti-6Al-4V material in the as-built and machined states fully met the requirements of ASTM F2924-14. By contrast, the ductility was compromised at oxygen levels above 0.2 wt.% (OS) in Ti-6Al-4V produced by EBM. Removal of the surface layer by machining increased the consistency and performance of the IS and OS Ti-6Al-4V materials. The fatigue behaviour of the EBM Ti-6Al-4V material was in the range of properties produced by casting. Due to the strong influence of both the surface finish and oxygen content on the fatigue strength, the IS Ti-6Al-4V material exhibited the highest performance, with results that were in the range of parts that had been cast plus hot isostatically pressed.