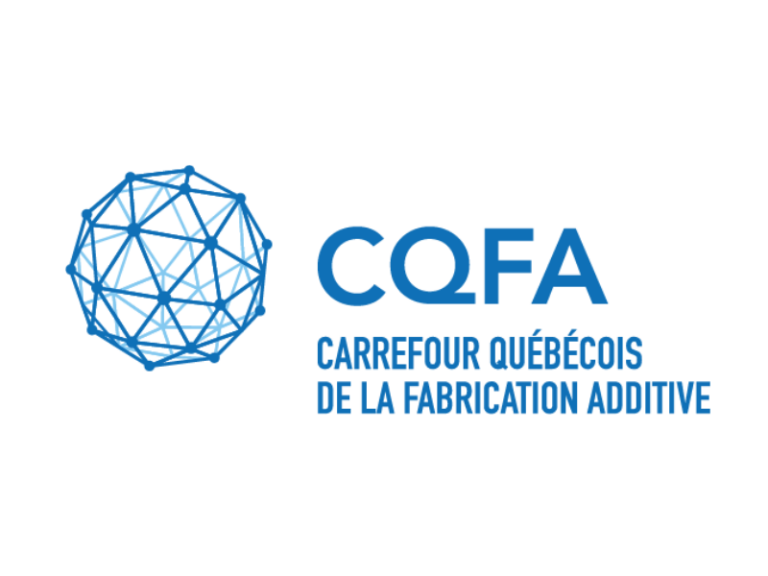
2023/01/12
Propriétés mécaniques et stabilité dimensionnelle des biocomposites fabriqués par impression 3D par extrusion de filament
Dammak, Y. (2022). Propriétés mécaniques et stabilité dimensionnelle des biocomposites fabriqués par impression 3D par extrusion de filament (Master’s thesis). Université du Québec en Abitibi-Témiscamingue.
The 3D printing process with fused deposition modeling (FFF) is continuously developing. Nevertheless, it has always been called by abuse of language the quick prototyping. Thus, a challenge of improving the low mechanical properties of the printed parts creates our project problem. In addition to this challenge, the strong tendency to substitute plastics for sustainable development draws attention to the
involvement of ecological materials in industrial life. In this perspective, the objective to develop bio-sourced composites for 3D printing by FFF is inscribed. The strategy followed to overcome the limited performance of the printed part is to create biocomposites with a polylactic acid (PLA) matrix loaded with fibers of (microcrystalline cellulose/biochar/spruce wood). Therefore, a series of biocomposite filaments were developed and printed after optimizing the parameters of the FFF printer. The specimens of the different mixtures are manufactured to test the following factors: 1) the type of filler; 2) the filler content; 3) the addition of treatment on the fibers; 4) the type of matrix. Then, a comprehensive study of the effects of these factors on the thermal, physical and mechanical properties of the specimens was carried out. The biocomposites with 5 % BC exceeded Young’s modulus of the printed raw polymer and the tensile strength. Also, fibers treatment improved the tensile and flexural strength while facilitating the processability of the material. The addition of 15 % CMC or EPN filler improves the tensile and flexural Young’s modulus but destroys the polymer’s performance on impact and moisture tests. Finally, a comparative analysis was concluded between the mechanical and physical properties of the specimens manufactured by 3D printing and injection molding. The injection molding products generally presented the best performances. But, against expectations, the deformation at break and the toughness of the printed composites reached the properties of the same formulas injected. The results are highlighted by microscopic observations that underline the structure of the specimens and the nature of the fiber/matrix interfacial bonding.